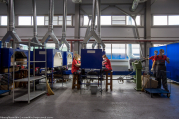
Как в русской провинции делают обувь


Давненько, дорогие друзья, я не выкладывал вам промышленные фоторепортажи. Исправляюсь! Не знаю как у вас, но у меня с детства существовало стойкое предубеждение по поводу отечественной обуви. Если некоторая одежда в позднесоветские "кооперативные" времена уже была более-менее, то обувь точно нет. И некрасивая, и разваливалась со временем. Казалось, что и сегодня ситуация ненамного лучше. Именно поэтому недавняя поездка на Торжокскую обувную фабрику стала для меня чуть ли ни откровением.
Торжок? Глухая провинция? Там ещё и обувь делают? Да как такое вообще может быть? Ладно, вот вам для начала вводные.
Торжокская обувная фабрика (ТОФ) входит в группу компаний "Восток-сервис" - это известнейший и один из крупнейших в Европе производитель спецодежды, спецобуви и средств индивидуальной защиты для людей рабочих профессий (всего 18 производств в России и за рубежом). ТОФ сегодня - это современное предприятие с новыми цехами, роботизированной техникой и оборудованием, ежегодно производящее более двух миллионов (!) пар обуви. Основные заказчики продукции — промышленные предприятия машиностроительной, энергетической, металлургической, строительной, нефте- и газодобывающей и перерабатывающей промышленности и так далее. Сегодня на ТОФ трудится 700 человек, средний возраст персонала – 28-30 лет.
Ну что же, давайте посмотрим, что представляет собой эта фабрика и как происходит процесс производства обуви.
1. Территория ТОФ выглядит так. Чистенько, аккуратненько и даже вполне себе симпатично в плане расцветки.

2. На фабрике живёт котик и я подозреваю, что он здесь далеко не единственный.

3. А вот и сам процесс производства. Перед нами кожаные заготовки, из которых в скором времени родятся ботинки и сапоги.

4. Всё компьютеризировано. Например, таким хитрым способом лоскуты кожи подготавливают к раскрою.

5. Затем на определённые участки с помощью лазерных головок проецируется схема раскроя.

6. Кожу раскраивают на автоматическом раскройном комплексе АТОМ.

7. Здесь выполняют выравнивание деталей по толщине.

8. Пошив заготовки верха.

9. После этого заготовки верха надевают на колодки.

10.

11.

12. Затем по специальной ленте "ласты" транспортируют к затяжной машине.

13. Предварительная установка подноска.

14.

15. Затяжка носочной части обуви на композитный или металлический подносок.

16. Удаление излишков затяжной кромки и выравнивание следа.

17. Следующим этапом идёт влажно-тепловая обработка.

18. После чего, перед отправкой в литьевой агрегат, обувь снимают с колодки.

19. А потом снова надевают, только уже на металлическую колодку агрегата.

20. А это процесс так называемого шершевания боковой поверхности заготовки верха обуви роботом и нанесение RFID-метки на стельку.

21. Прилив подошвы.

22. Отделка.

23.

24. Затем обувь комплектуют инструкцией по эксплуатации.

25. Ну тут и так ясно.

26. И под занавес, как водится - контроль ОТК.

Вот такой процесс. Если честно, я был приятно удивлён.
Всё самое интересное и оперативное я публикую здесь, подписывайтесь:




НУ И ДОБАВЛЯЙТЕСЬ В ДРУЗЬЯ!
|
</> |
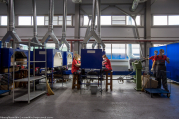