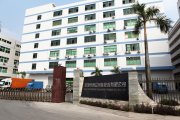
Чип в корпусе ДИП: дешево и сердито


- Во-первых дизайнхауз (design house). В нем микросхемы придумывают и конструируют. Сейчас микросхемы содержат миллионы транзисторов, поэтому дизайн-хауз оперирует не отдельными элементами, а целыми блоками. Фактически он только соединяет уже кем-то разработанные ранее модули (IP-блоки) в единое решение. Например, широко известный процессор ARM - это всего лишь IP блок, хоть и очень сложный. ARM не продает процессоры, он торгует лицензиями на использование своих разработок.
- Во-вторых фаундри (foundry). Это завод, который изготавливает микросхемы по заказу дизайн-хаузов. Микросхемы формируются на круглых кремниевых пластинах диаметром 100, 150, 200 или даже 300 милиметров. Крупнейший в мире производитель микросхем - тайваньский TSMC (вы вообще слышали про такого?) работает именно по схеме фаундри.
- В-третьих фаблесс (fabless) производители. Это чаще всего дизайнхауз, сам продающий свои разработки, но не имеющий производства. Так, крупнейший мировой производитель процессоров для мобильных телефонов - американский Qualcomm - классический fabless, размещающий заказы на том же TSMC.
- Ну и четвертый вид игроков на этом рынке - упаковщики. Дело в том, что полученные от фаундри кремниевые пластины на плату не впаяешь - их сначала нужно нарезать на отдельные микросхемы и поместить в какой-то корпус. Собственно этим и занимаются упаковщики. На этот процесс мы и пойдем с вами сейчас.
Производство довольно компактное - занимает три нижних этажа здания.

Поступающие пластины - а здесь работают только с пластинами до 200 мм, хранятся в
среде азота в специальных шкафах.

Подготовительный этап - пластины утоняют на шлифовальных станках с 500 до 200-300 микрон и нарезают на отдельные микросхемы. Чтобы диск не поломался, его устанавливают на специальную растяжку.
Нужно сказать, что в чистые помещения меня не пустили, поэтому, чтобы увидеть крупные планы пластин, вам придется немного погуглить.

Затем микросхемы, одна за одной, переносятся на рамки с выводами.

Вот покрупнее, но все равно не сильно понятно. Пластина - это круг правее внизу. Над ним завис вакуумный захват. Слева два шприца дозатора клея.

Это ряды машин, на которых чип соединяется с металлическими выводами рамки. Соединение делается золотыми или медными проводниками, а сварка производится ультразвуком, если ничего не путаю.

Переходим в цех литья.

Рамки с наклеенными чипами приходят сюда в специальных контейнерах.

Вот так получше видно.

Здесь отливаются пластиковые корпуса микросхем. Слева робот для загрузки рамок на оснастку. Справа - пресс для литья (процесс называется transfer molding). А на столе перед нами - готовые отливки.
Давайте чуть поподробнее.

Вот робот раскладывает рамки на хитрую оснастку.

Вот в другую приспособу помещаются таблетки пластика.

Оператор закладывает оснастку в пресс-форму, и одним движением сбрасывает все таблетки в специальные гнёзда формы.

Форма разогревается, и толкатели расплющивают наши таблетки, продавливая расплавленный пластик по литниковым каналам к корпусам будущих микросхем.

Через каждые 600 циклов пресс-форму надо чистить. Для этого делают запрессовку силиконовой резины. Да-да, той самой резины.

Вся грязь липнет к силикону.

Следующий этап - на микросхему нужо нанести надписи. Лазерная гравировка.

Тоже гравировка, но автоматическая.

Ну и последний этап - вырубка микросхем из рамки.

Обычный пресс, ничего особенного.

После вырубки микросхемы ссыпаются в линейки-пеналы.

Ах да, еще нужно перепаковать их в ленты, чтобы при монтаже на плату автоматический установщик мог их захватить.

Чего-то я уже утомился, а тут еще контроль качества.
Контроль геометрии.

Визуальный контроль. Люди в розовом.

Рентгеновский контроль.

Теперь вроде всё. Да, забыл сказать, что завод пакует в корпуса DIP-8, SOT-23, SOP-8 и SOP-16. Класс чистых комнат - 10 000.
Должен признаться, что я не большой специалист в упаковке микросхем, прошу очень сложных вопросов не задавать :))
|
</> |