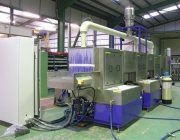
"Значение по умолчанию", или "ТРИЗ в действии, эпизод 1"

Хотя придумана "теория решения изобретательских задач" была в СССР, в далеком 1956 году.
Для ознакомления всем, и взрослым, и особенно детям - рекомендую очень хорошую советскую книжку
Генрих Саулович Альтов "И тут появился изобретатель". (Альтов - это псевдоним Альтшуллера, который собственно ТРИЗ и изобрел).
Примерчик оттуда: вот как, по-Вашему, сделать шоколадную конфету с жидкой начинкой?
Вариант "в лоб": отливаем оболочку (кондитеры говорят "корпус") конфеты, в нее отливаем начинку, и сверху запечатываем крышечкой.
Хорошо? Замечательно, но нужно аж три разливочных машины. Которые стОят денег, занимают место и потребляют электричество (и запчасти).
Можно ли проще? Покумекайте чуток. Ответ под первым катом.
Отливаем начинку в нужную форму. Замораживаем до минус 18. Начинка становится твердой. После чего обливаем ее жидким шоколадом.
Теперь нам нужна всего одна разливочная машина. И одна ванна с шоколадом, которая проще-дешевле.
Уж не знаю, читали ли немцы советские детские книжки, но они делают конфетные линии в том числе и с именно такой технологией.
Скажете, что все это нужно только каким-то там немецким конструкторам? А нормальным людям нечего и голову забивать такой ерундой?
Это... как посмотреть.
Потому что есть еще такой почти-универсальный почти-закон природы.
Чем лучше работаешь головой - тем меньше понадобится работать руками-ногами.
Вот вам еще примерчик, из обычной-повседневной фабричной жизни.
Как известно, в любом нормальном пищевом производстве (нормальном, а не таком, как вот тут), все, что касается собственно продукта и не только, надлежит периодически мыть.
В частности, те самые вышеупомянутые формы, в которые конфетки отливаются.
Поскольку форм много, моют их не руками, а в весьма продвинутой туннельно-конвейерной моечной машине. Вот примерно в такой:
![Значение по умолчанию, или ТРИЗ в действии, эпизод 1 marr_1[1].jpg](http://ic.pics.livejournal.com/fixik_papus/75163700/3373/3373_600.jpg)
(фото взято отсюда, там же можно и почитать о промышленных моечных машинах, кому интересно)
Машина умеет мыть паром, химией и ультразвуком любые формы, какие только есть на производстве.
Формы бывают разной формы (простите за тавтологию), размера и веса. И каждый вид форм нужно положить на цепной конвейер правильным образом.
На немецкой фабрике к моечной машине уже приставили роботов, у нас же на текущий момент (и обозримое будущее, увы) это делается вручную.
Иногда мойщики кладут форму "не так". После чего ее заклинивает внутри машины, форма ломается и гнет лопатки конвейера и все вокруг, до чего дотянется.
После чего машину нужно разбирать, выковыривать обломки и править погнутое железо. Основная проблема даже не в том, что формы жалко; а в том, что мойка задерживается, без форм вымытых конфетная линия работать не может, а внеплановый простой линии - это уже совсем нехорошо.
Через некоторое время и несколько случаев стало ясно "нужно что-то делать".
Как-то раз механики зовут меня на участок мойки.
- Вот смотри, мы тут хотим сделать механизм, чтобы криво засунутые формы внутри машины выравнивать нужным образом. Механику мы уже придумали, а управление ей сделать - это по твоей части.
Смотрю на эскизы. "По моей части" - управление четырьмя пневмоцилиндрами. А это
- пневматика - собственно пневмораспределители, трубки, дроссели и прочая
- управление ими с дискретных выходов - кабели до ближайшей стойки распределенной периферии и модуль вывода в нее добавить.
- контроль положения их - восемь датчиков Холла, кабели и модули ввода
- контроль положения форм - два или три датчика, кабели и модули ввода (плюс поломать голову, куда поставить, и учесть, что это внутри моечной машины и нужно спец.исполнение)
- синхронизация с положением цепи, чтобы выравниватели сами цепь не ломали
- логика управления всем этим безобразием в контроллере, в автомате и вручную
- соответствующие картинки и настройки на панели
- подрисовать все изменения в схему
- подписать в инструкцию для операторов
Дел намечается вдвоем на целую смену. Это если на фабрике за всю смену ничего не сломается и не придется отвлекаться. А такого не бывает, посему нужно класть две смены. Не забываем добавить универсальный инженерный коэффициент, в данном случае - пи пополам. Итого - возня на три смены гарантирована.
Тут у меня в голове включается встроенный индикатор лени и напоминает о почти-универсальном почти-физическом законе (см. выше).
Не попробовать ли поискать более простое решение проблемы?
Начнем сначала. Нужно сделать, чтобы криво лежащая форма внутри машины ничего не ломала; и была сигнализация "достань и положи как нужно". Достать, например, можно штатной кнопкой реверса конвейера. А тормозить/сигнализировать - по превышению момента на приводе главной цепи.
К счастью, мотор крутится частотником. Смотрю его настройки - уставка ограничения момента стоИт по умолчанию для мотора данной мощности. Мощность мотора (и момент), очевидно, соответствует самым большим-тяжелым формам. Для форм поменьше - мощи хватает переломать все нафих. Вот нам и способ - подобрать уставку останова по превышению момента для каждого вида форм индивидуально.
Тут работы намного меньше. Частотник подключен к контроллеру по Profibus, замечательно. Меняем стандартную телеграмму PZD-2/2 (где на частотник идет только команда и уставка скорости) на PZD-6/6 (чтобы еще и момент с контроллера задать). Добавляем в набор параметров формата на панель еще одну цифирьку и вытаскиваем ее на панель. Умышленно запихивая в машину разные формы разными кривыми способами (руками механиков, разумеется) - подбираем нужные настройки. Аварийная сигнализация останова по превышению момента имеется штатная, остается только прописать в мануал - в случае чего жмем "сброс", потом "реверс", достаем форму, кладем "как надо" и жмем "пуск". Все, проблема закрыта.
На все эти действия ушло времени меньше, чем на написание поста о них.
Затраты - строго равны нулю. Ни одной новой железки в машине не добавилось, а рабочее время... так я все равно на смене.
(А уж как механики-то рады!)
Мораль: сначала думаем. Потом делаем. Чем лучше думаем - тем быстрее и лучше сделается.
|
</> |
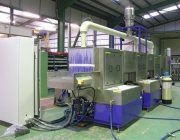